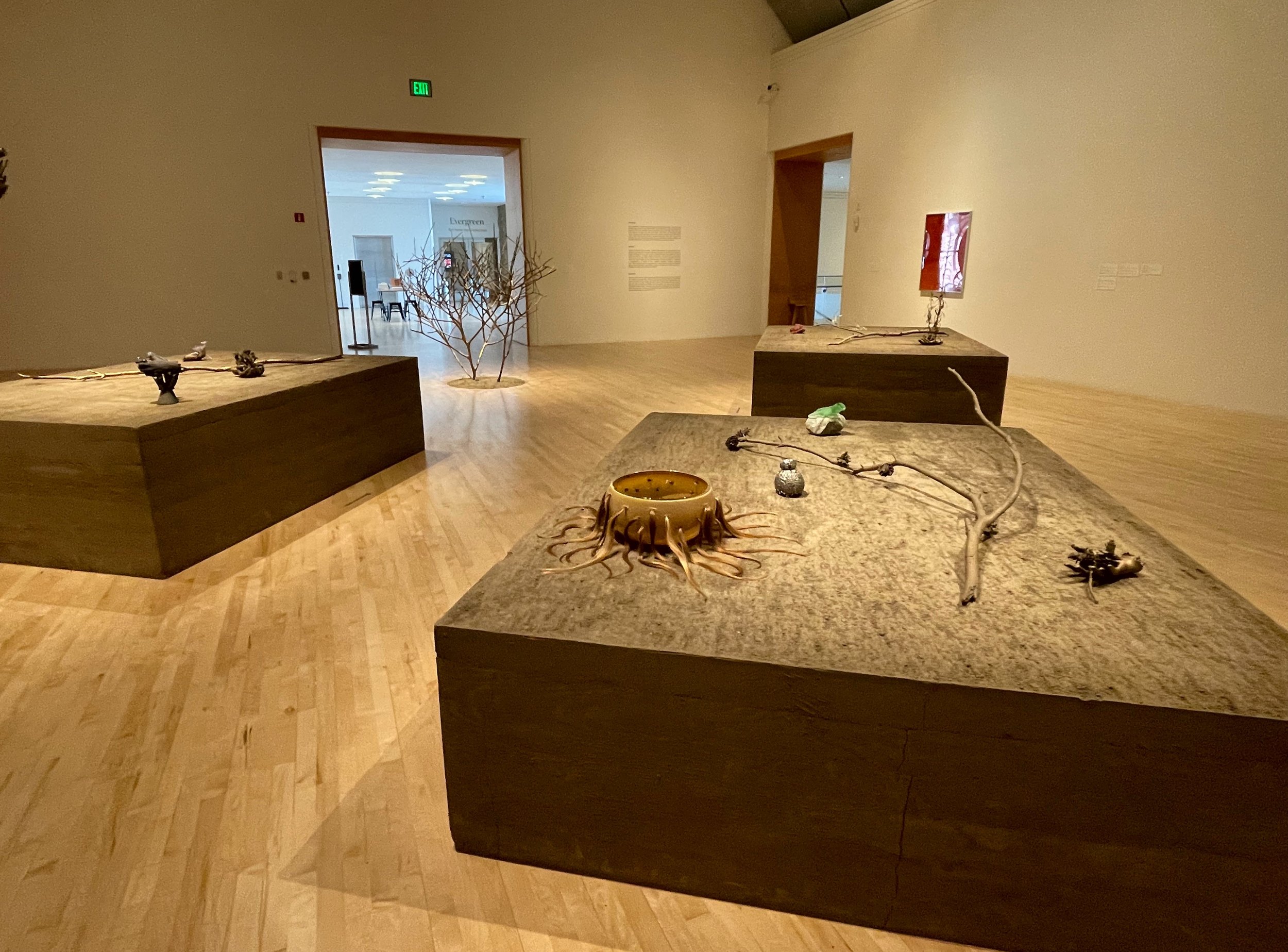
Rammed Earth
Project Management: Complex Exhibition Installation
A challenging project that required months of planning, unique vendor sourcing, specialized equipment acquisition, and some innovative solutions involving precise coordination of multiple teams. This project demonstrates my ability to execute on complex plans while leading teams through unique technical challenges.

Material
Acquisition
Custom soil blends aren’t that easy to get. To facilitate the ask of 5 tons of sifted soil pre-mixed with 10% Portland Cement, I conducted a California-wide search of soil farms and aggregate suppliers and met with multiple sources to talk about how they could meet these specialized needs.
Of the 20+ vendors I contacted, only one could meet the requirement. Adding complexity, we could not use their delivery service because it would hamstring our loading dock for weeks.
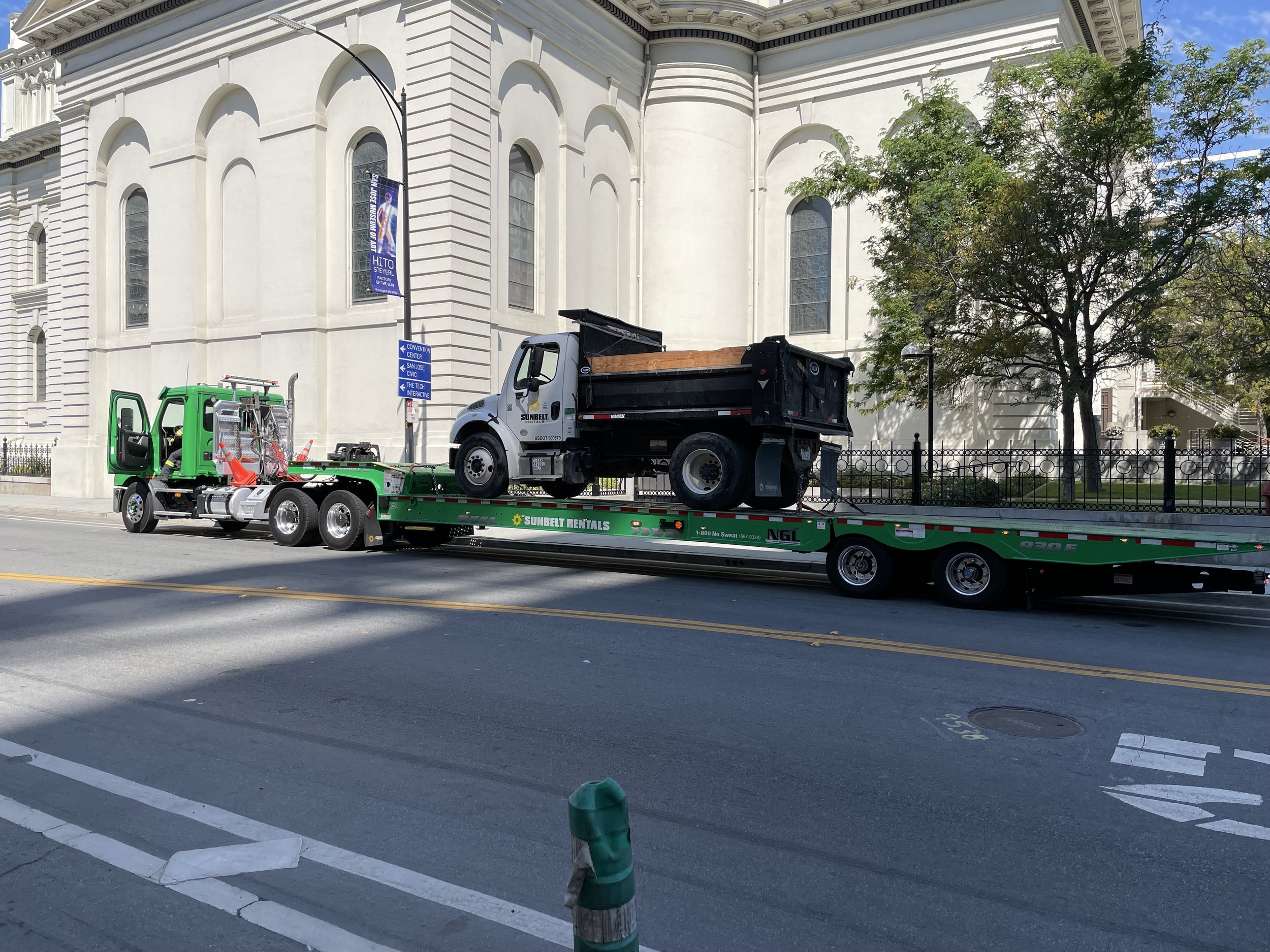
Logistics Coordination
I organized transportation and delivery of 8 tons of soil by renting a dump truck and drove it to the coast to pick up the soil.
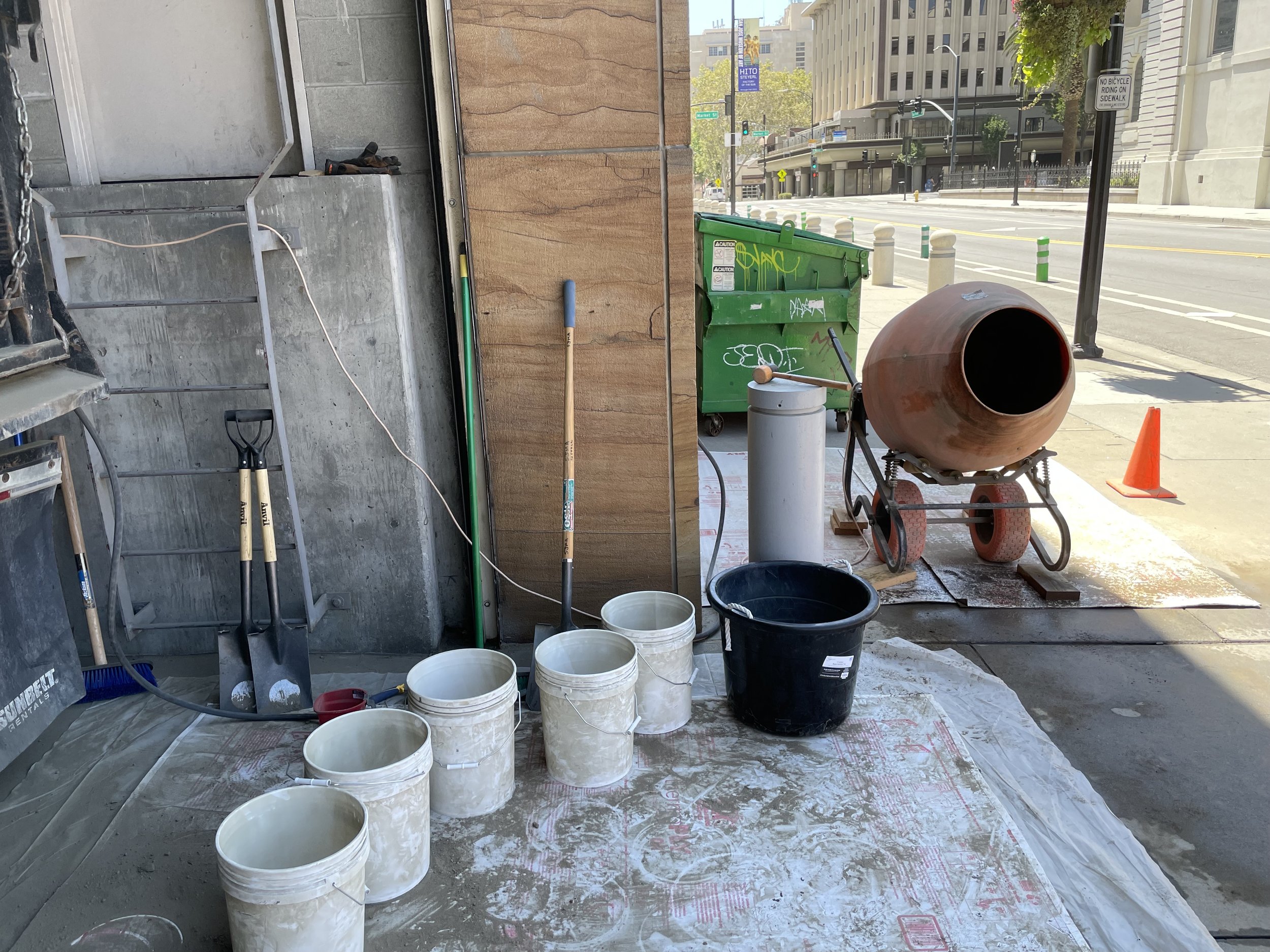
Operational Strategy
I developed and executed a plan to convert our loading dock into a rammed-earth production facility. To do this, I rented a concrete mixer and set up a soil mixing station. To avoid having to lift the heavy buckets of wet concrete to the dock level, I rented a fork lift and built a small ramp on a palette to use as a bucket elevator. Mixed buckets could now be moved on dollies for their entire long path to the forms on the second floor where each bucket was poured and “rammed” into the form.
Effectively converting our facility to a rammed earth factory for 3 weeks emphasizes the unique operational aspects of large scale art museum projects. Extensive protection of infrastructure, teams on 2 floors, and many moving parts made this a very complex and dirty operation.
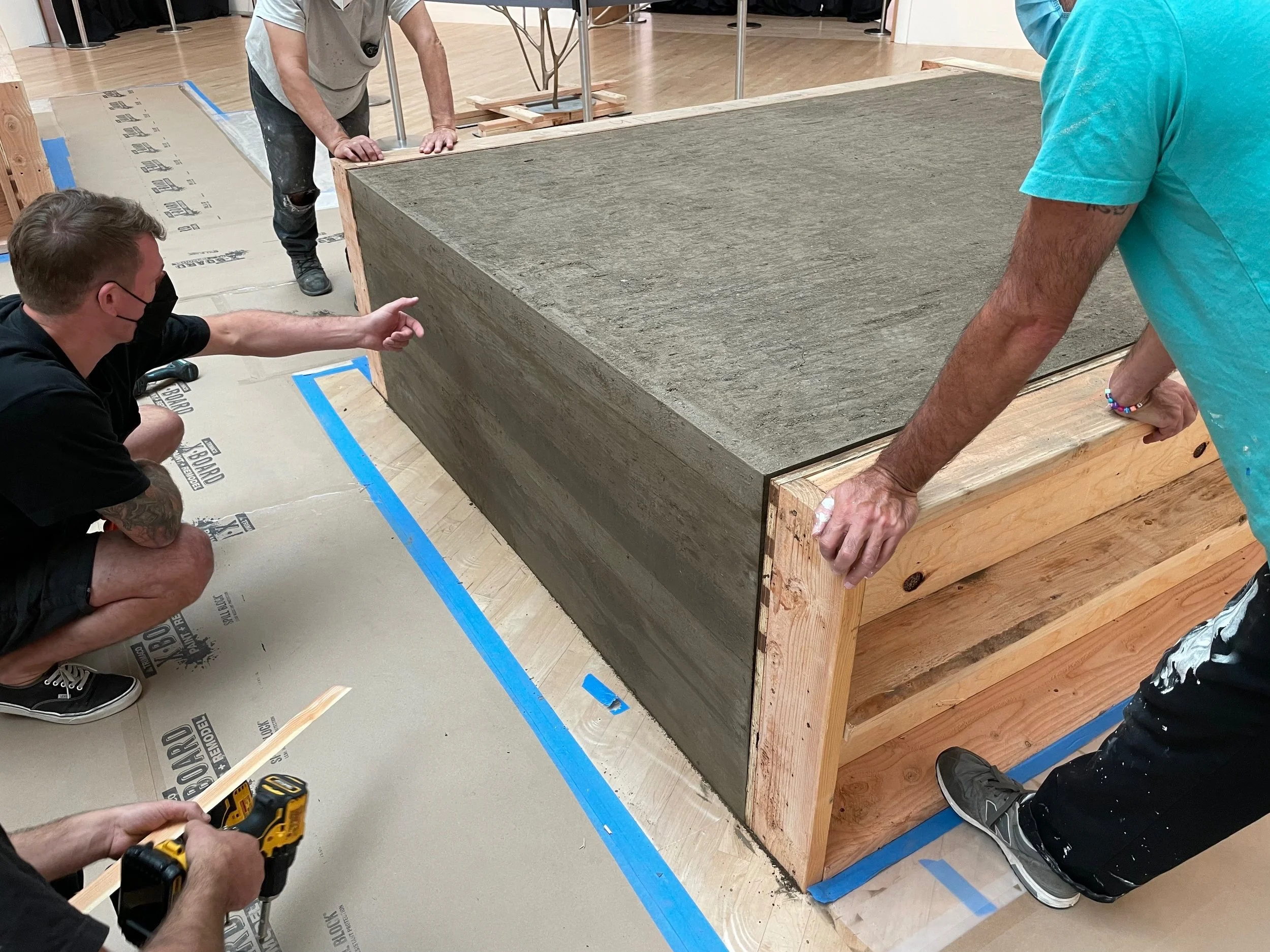
Team Leadership
A big challenge here was maintaining quality standards, operational safety, and energy levels throughout the construction phase. A 10-person team including 3 outsourced specialists on 2 floors with constant movement and physical demands is fundamentally difficult.
To successfully manage this, I coordinated and controlled timing and workflow from the dock mixing station. This was about as far from the mold pouring and final “product” as you could get - but our 3 outsourced contractors were there specifically to “ram the earth” and as it turned out controlling the proper speed and quantity of bucket delivery was the critical aspect of filling these forms correctly.
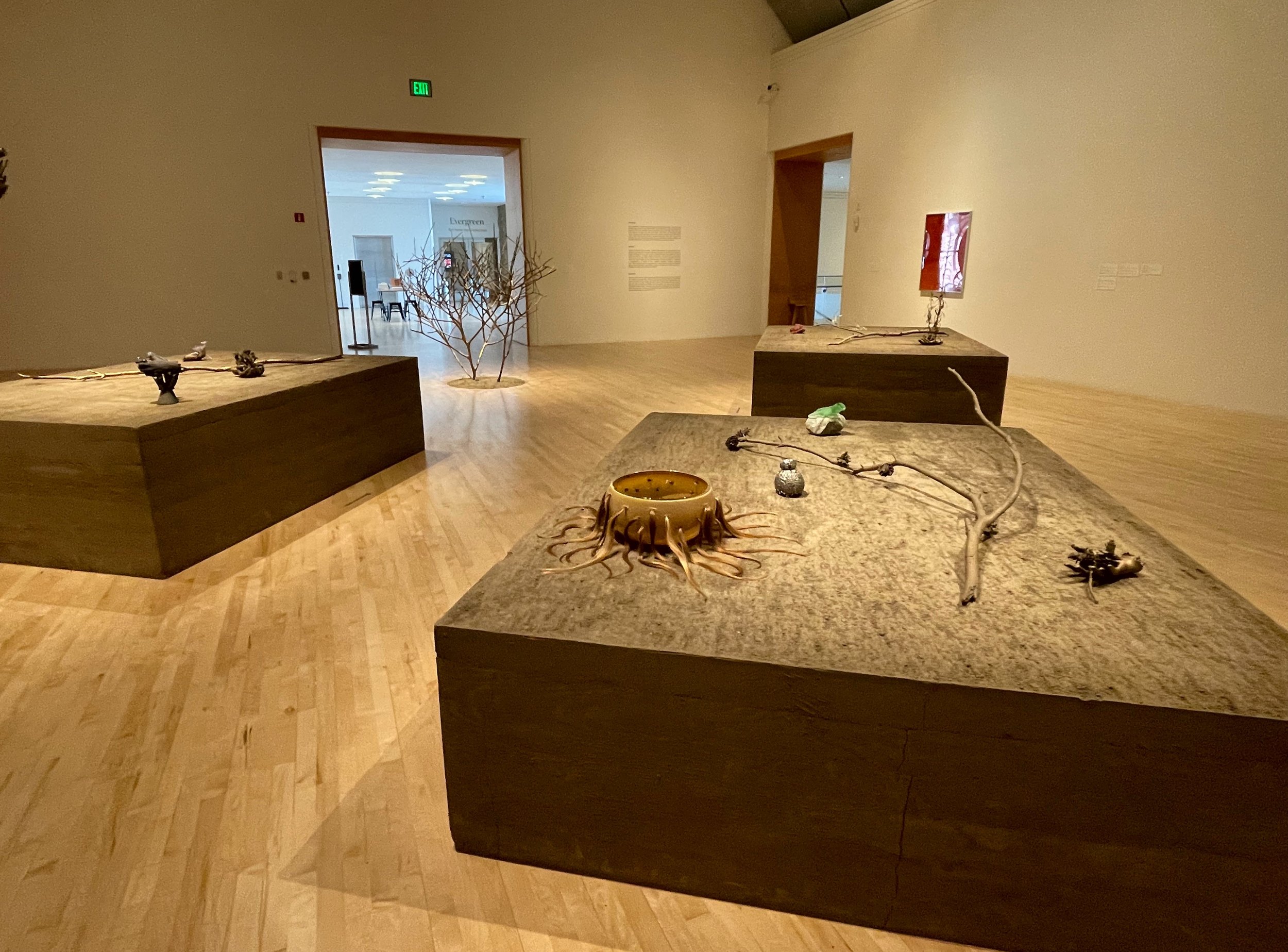
Driving Successful Outcomes
This project highlights my agile approach to project management, and my ability to develop practical solutions to unique and complex challenges through careful planning and effective team coordination.
The successfully installed rammed-earth pedestals met all technical specifications and aesthetic requirements and were completed ahead of schedule.